Channel Coating Pots
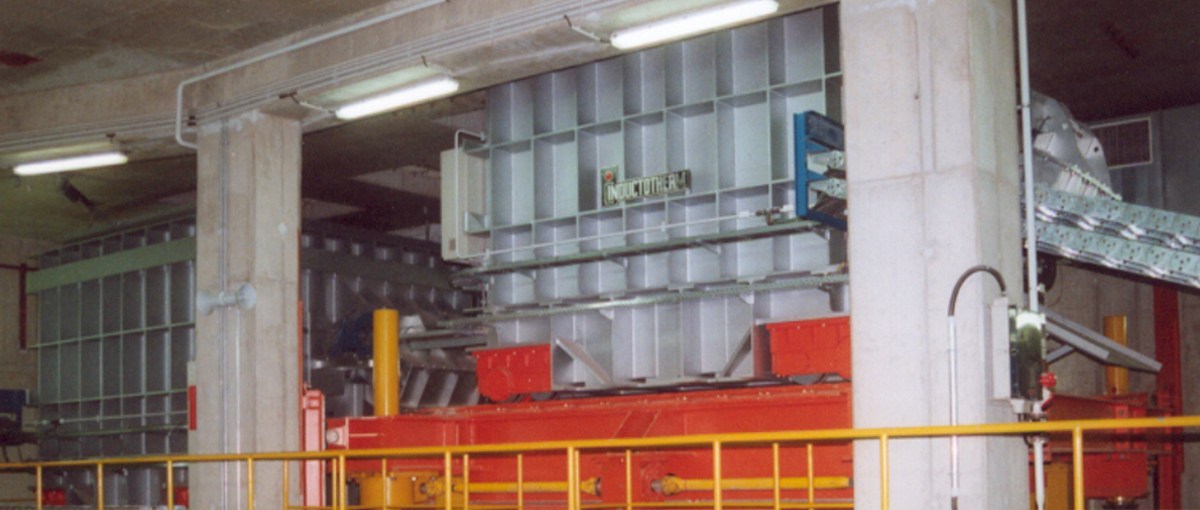
Inductotherm Channel Coating Pots are used by the steel industry for the continuous coating of steel strip.
Features
Channel Coating Pots provide good inductor refractory life making them ideal for galvanized, galvannealed and Galfan® coatings. They are also used for aluminum zinc and other aluminum alloy coatings. Channel inductors contain induction coil assemblies and a magnetic core made of special transformer sheet laminations. These pots are designed to hold very large volumes of metal. Inductotherm Channel Coating Pots feature:
- A rectangular design to allow for large volumes for direct ingot feeding
- Heavy gauge steel plates for excellent refractory support
- Temperature monitoring to enhance reliability
- On-site preparation with custom dry rammed refractory around a consumable channel mold (can be hung within 24 hours of installation)
- Optional bogies and lifts for multiple pot installations
- Water-cooled or air-cooled inductors
Galfan® is a trademark of Galfan Technology Centre, Inc.
Tech Specs
Capacities | Large Capacity Continuous Coating Lines |
Small Capacity Hot-Dip Batch Coating | |
Standard Features | Water-Cooled Twin Loop Inductors up to 750 Kilowatts |
Air-Cooled Twin Loop Inductors up to 500 Kilowatts | |
Hybrid Water and Air-Cooled Inductors up to 500 Kilowatts | |
Inductor Flange Metal Leak Detection | |
Single-Phase Tap Changer Power Supply Units up to 500 Kilowatts | |
Three-Phase Balanced Tap Changer Power Supply Units up to 500 Kilowatts | |
Solid-State VIP™ Power Supply Units with SCR Technology up to 750 Kilowatts | |
Solid-State VIP™-I™ PWC Power Supply Units with IGBT Technology up to 500 Kilowatts | |
Water Cooling Systems with Emergency Backup | |
Molten Metal Leakage Detection | |
Power Pulsing Circuit | |
Patented Hollow Metallic Channel Mold for Zinc and Zinc-Aluminum Alloy Applications | |
Optional Features | Metal Level Measurement and Monitoring |
Remote Control Consoles for Remote Operation from a Central Pulpit | |
PLC Controls and Communication Options Available on VIP™ and VIP™-I™ Power Supply Units | |
Emergency Power and Changeover Systems | |
Inductor Covers | |
Insulated Pot Covers | |
Moveable Pot Designs for Multi-Pot Installations | |
Pot Lifting Systems for Multi-Pot Installations | |
Automated Robotic Dross Removal Provided by the ARMS™ System | |
Factory Tested | Critical Components |
Available Retrofit Options | Molten Metal Leakage Detection |
Communications Options via a Variety of Industrial Protocols | |
Power Pulsing Circuit | |
Automated Robotic Dross Removal Provided by the ARMS™ System |