Vertical Steel Induction Billet Heating Systems
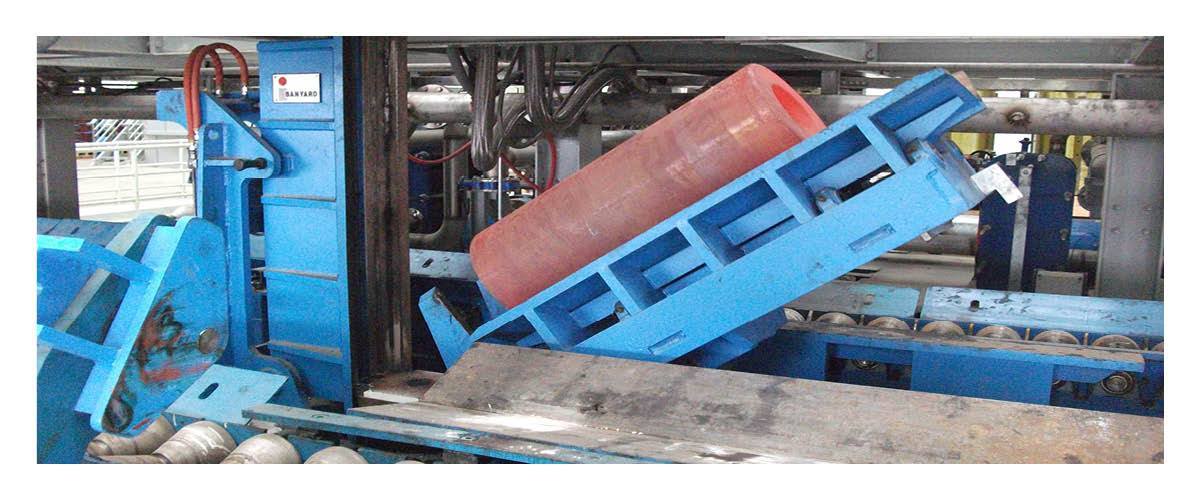
Banyard engineers have responded to this challenge, applying over 40 years design and manufacturing experience gained from specialist induction heating applications. As a world leader in the design and manufacture of Low Frequency Induction (LFI) power supplies, Banyard also offers customers extensive electrical control and mechanical handling expertise, delivering turnkey solutions. The result is Vertical Steel Billet Heating systems (VSI) , offering the latest in proven technology whilst delivering fast, accurate and highly repeatable induction heating of steel billets. Banyard turnkey Vertical Steel Billet Heating systems offer customers total reliability and low maintenance costs prior to the extrusion process.
This has been brought about by increased market requirement for high integrity tubing having a totally uniform, homogeneous metallurgical structure. Seamless tubing extruded from 304 / 316 stainless steels and special alloys such as Inconel provides excellent anti-corrosion protection and higher pressure containment in the absence of a weld seam, making it ideal for use on demanding aerospace, petrochemical, marine, power generation, dairy and pharmaceutical applications.
Banyard Vertical Steel Billet Heating systems are designed for precision vertical induction heating of solid or pierced billets and tubes with diameters over the range 150mm to 460mm, and lengths between 300mm and 1500mm.
Billet Up-Ender / Charger Unit
Pre-heated billets are discharged sideways to the heating station up-ending units by pusher to a transfer ramp from the cold billet shuttle conveyer. The transfer ramp holds the billet, awaiting the control signal for the billet heating to commence. The transfer ramp then loads the billet into the up-ender. This orientates the billet in a vertical mode and inserts it into the vertical induction coil via a hydraulic lifting ram. The hot billet is then lowered and discharged sideways onto the hot billet trolley conveyer. An adjustable lifting ram accommodates different billet sizes.
PLC System and Operator Interface
A standard PLC control system is provided based upon Siemens S7 series components for the control and sequencing of all induction heaters (pre-piercing, and pre-extrusion), conveyors and up-ending / charging units.
The system includes distributed I/O at the individual heating stations and an operator console which can be located at the press operator’s position. The operator’s terminal includes an HMI panel for entry of production parameters and system status display.
Minimising Oxidation (Scale)
Top hat assembly is mounted on top of the coil to significantly reduce heat loss and to provide containment for controlled atmosphere heating of carbon steels. Inert gas ports are provided at the base of the coil.
Controlled atmosphere induction heating of pierced billets results in significantly less oxidation and scale when compared to gas heating.
Features
Banyard Vertical Steel Induction (VSI) systems have been designed for the precision vertical induction heating of solid or pierced billets:-
- Billet diameters over the range 150mm to 460mm
- Billet lengths 300mm to 1500mm
Banyard also offers customers extensive electrical and mechanical handling expertise, able to deliver complete turnkey solutions including the following:-
- Billet Up-Enders / Vertical Lift Units
- Billet Transfer Ramps / Conveyors
- Billet heating in controlled atmosphere systems to minimise unwanted oxidation
Benefits of single-shot VSI technology
- High circumferential temperature accuracy and repeatability. i.e. better temperature distribution.
- Automated coil tap variations for different billet lengths giving the ability to vary the temperature profile along the billet length.
- Ability to process billets from different materials with minimum oxidation and scale (by controlled atmosphere technology).
- No billet sticking.
- No glass lubricant build-up.
- Flexibility of operation
- Single-zone systems with automated coil tap variations for different billet lengths giving the ability to vary the temperature profile along the billet length
- Multi-zone systems with zone control and switching for different billet lengths giving the ability to vary the temperature profile along the billet length
Tech Specs
- Temperature Considerations
- To ensure that temperature accuracy is linear along the length of the billet, specially designed laminated flux concentrators are positioned above and below every billet within the induction coil.
- The positions of these flux concentrators are relative to the billet, its position within the induction coil controls and the end temperature of the billet.
- Two optical pyrometers are provided to closely monitor the maximum surface temperature of the billet, providing a fail-to-safe temperature check policeman.
- Overall temperature repeatability of +/- 15⁰C can be achieved with point to point temperature guaranteed to be within 5%.
- Maximum surface temperature is always taken into account before determining the optimum applied power / heating curves for a specific billet size.
- Depth of heat penetration on billet surface increases at lower frequencies. To ensure maximum productivity and optimum operating conditions are achieved, the frequency can be varied.
Flexibility exists for raising the billet-end temperature in order to overcome radiation losses.
- VIP power inverter specifications
- Power rating: 500kW to 1000kW
- Supply: 400V 3-Phase, 575V 6-Phase (depending on power required)
- Power factor: 0.95 Efficiency >95%
- 0 to 100% step-less power control
- Adjustable frequency 50 to 150Hz